Finding the Right EMI Shielding Fingerstock EMI Gasket For You
Parker Chomerics beryllium-copper (BeCu) and stainless steel SPRING-LINE® branded EMI gaskets combine high levels of shielding effectiveness with a broad deflection range and low closure force properties. The spring finger wiping action can also help to reduce oxide build-up at mating contact surfaces when the gasket is used in applications demanding repeated openings and closings. The excellent performance qualities of beryllium-copper, including: high tensile strength, extreme operating temperature range and superb electrical conductivity, make it an ideal material for EMI shielding over a broad frequency range.
For applications that are mechanically less demanding, stainless steel gaskets offer good tensile strength, extreme operating temperature range and good electrical conductivity. Stainless steel gaskets have higher compression set than BeCu, when used in demanding applications.
We offer BeCu shielding gaskets in four standard finishes: clean and bright (unplated), zinc / clear trivalent chromate, bright nickel, and bright tin. These four finishes are RoHS compliant. Other common finishes are are available upon request. BeCu gasket finishes should be chosen to minimize galvanic corrosion of the final assembly.
What About Corrosion?
Galvanic corrosion occurs as electrons move from dissimilar metals through an electrolyte, such as water or salt spray / fog. The goal of an EMI gasket is to be part of an electrically conductive shield and the gasket material is typically mated with a structural metal, such as aluminum or stainless steel. Since BeCu or stainless steel EMI gaskets are galvanically different than aluminum or steel, there would be two dissimilar metals in contact with each other. If the assembly in the application is susceptible to the presence of an electrolyte, there is a high probability that galvanic corrosion will occur, which will degrade both the structure and the shielding effectiveness in the application. To reduce the potential for corrosion, the electrical potential difference between the two metals should be minimized.
This is where the availability of different finishes on BeCu parts can help. For example, bright and clean BeCu parts in contact with chem filmed aluminum will typically corrode less if they are finished with tin plating. Nickel plated aluminum parts will work well with nickel plated BeCu. As an added bonus, among the current finishes we offer, nickel plating is also very abrasion resistant. Those applications with a lot of wear or many cycles could benefit from a nickel finish. Against zinc plated steel and zinc castings, the use of zinc/clear trivalent chromate parts is often used. See the Electromechanical Compatibility Table 3 on page 4 of the Fingerstock Selector Guide for further details.
Get More Information
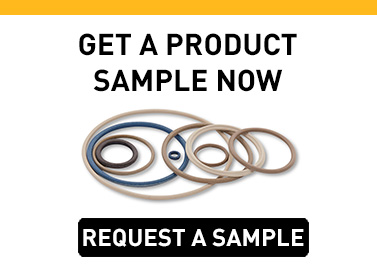
Easily test your application with a free sample